This article describes the connector plating used by J&B Electronics, the row of copper pins and the row of female contacts are manufactured from high quality copper alloys, a cost-effective, easy-to-manufacture material with good electrical properties. Metal plating is added to the core pins or contacts to allow or improve:
- Corrosion resistance
- abrasion resistance
- solderability
- Electrical Performance
- temperature protection
- exterior condition
All lead 1 pins and contacts are plated with a layer of nickel to:
- Provides resistance to abrasion and corrosion
- Prevents material migration between the substrate and the plated layer
Surface plating is available in full gold or ROHS compliant tin:
- Tin has excellent solderability and conductivity, but low durability – low cost
- Gold plating provides excellent electrical conductivity, low resistance, excellent corrosion resistance and durability – High cost
- J&B’s flash gold plating offers a good balance between the advantages of gold and the low cost of tin.
Currently, J&B offers the following types of plating:
- Full gold plating on the surface, nickel plating on the bottom: gold plating thickness of 0.6u”-30u” or higher is optional, nickel base is generally in the 30u”-60u”
- Surface fully tinned, bottom nickel plated: tin plating thickness is generally between 80u’-200u”, tin can be selected zero tin or Bright tin; nickel bottom is generally between 30u”-6Ou’.
- Surface plating half gold tin: and the contact point of the female chassis place gold plating, and PCB board soldering part of the tin plating, this way to balance the cost and performance requirements, half gold tin is generally used in the higher requirements of the product
- Silver plating: Surface plating according to customer requirements
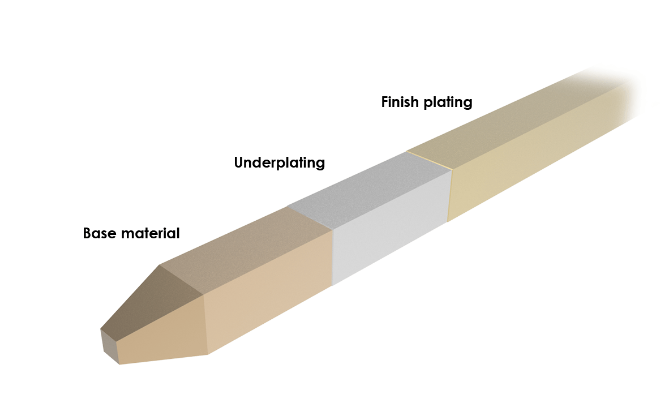